01
Series 90 Axial Piston Pumps Technical Information General
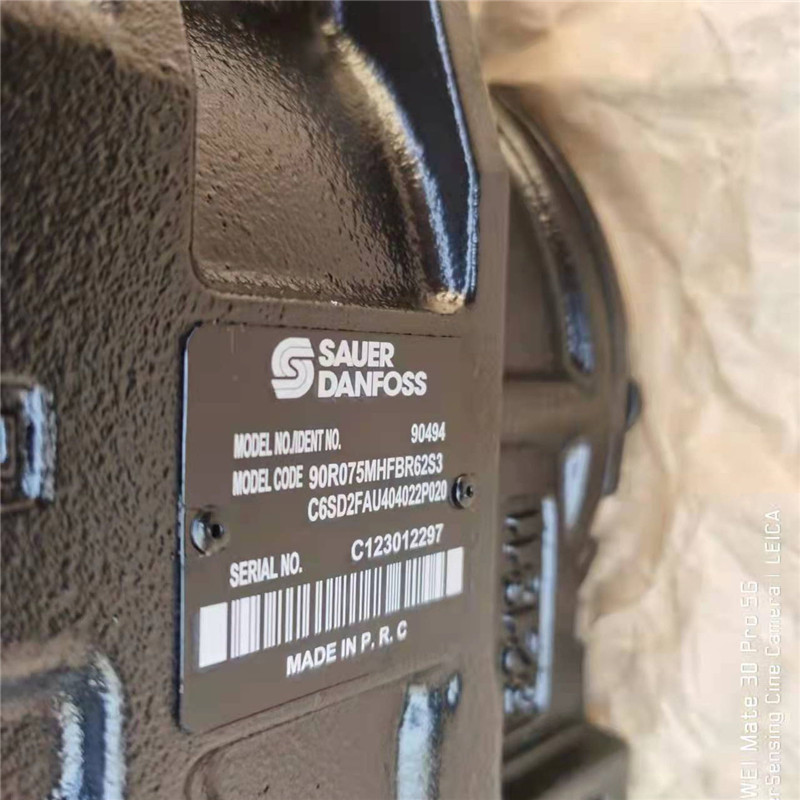
04
7 Jan 2019
Series 90 variable displacement pumps are compact, high power density units. All models utilize the parallel axial piston/slipper concept in conjunction with a tiltable swashplate to vary the pump’s displacement. Reversing the angle of the swashplate reverses the flow of oil from the pump and thus reverses the direction of rotation of the motor output.
Series 90 pumps include an integral charge pump to provide system replenishing and cooling oil flow, as well as control fluid flow. They also feature a range of auxiliary mounting pads to accept auxiliary hydraulic pumps for use in complementary hydraulic systems. A complete family of control options is available to suit a variety of control systems (mechanical, hydraulic, electric).
Series 90 motors also use the parallel axial piston/slipper design in conjunction with a fixed or tiltable swashplate. They can intake/discharge fluid through either port; they are bidirectional. They also include an optional loop flushing feature that provides additional cooling and cleaning of fluid in the working loop. For more information on Series 90 motors, refer to Series 90 Motors Technical Information 520L0604.
04
7 Jan 2019
A wide range of Series 90 controls and sensors are PLUS+1™ compliant. PLUS+1 compliance means our controls and sensors are directly compatible with the PLUS+1 machine control architecture. Adding Series 90 pumps to your application using PLUS+1 GUIDE software is as easy as drag-and-drop. Software development that used to take months can now be done in just a few hours. For more information on PLUS+1 GUIDE, visit www.sauer-danfoss.com/plus1.
Series 90 pumps can be used together in combination with other Sauer-Danfoss pumps and motors in the overall hydraulic system. Sauer-Danfoss hydrostatic products are designed with many different displacement, pressure and load-life capabilities. Go to the Sauer-Danfoss website or applicable product catalog to choose the components that are right for your complete closed circuit hydraulic system.
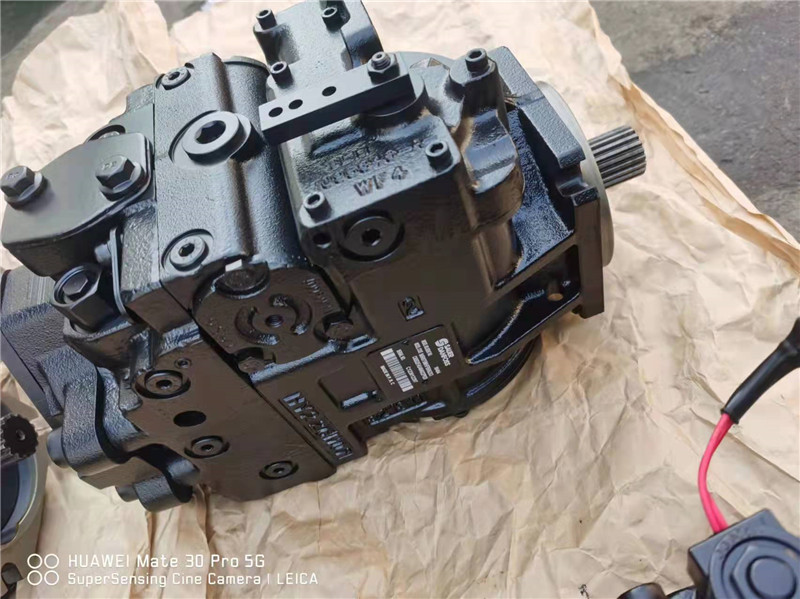
04
7 Jan 2019
Minimum speed is the lowest input speed recommended during engine idle condition. Operating below minimum speed limits the pump’s ability to maintain adequate flow for lubrication and power transmission. Rated speed is the highest input speed recommended at full power condition. Operating at or below this speed should yield satisfactory product life. Maximum speed is the highest operating speed permitted. Exceeding maximum speed reduces product life and can cause loss of hydrostatic power and braking capacity.
Never exceed the maximum speed limit under any operating conditions. Operating conditions between Rated speed and Maximum speed should be restricted to less than full power and to limited periods of time. For most drive systems, maximum unit speed occurs during downhill braking or negative power conditions. For more information consult Pressure and Speed Limits, BLN-9884, when determining speed limits for a particular application. During hydraulic braking and downhill conditions, the prime mover must be capable of providing sufficient braking torque in order to avoid pump over speed. This is especially important to consider for turbocharged and Tier 4 engines.